магазин
clinker cooler and finish grinding
KEFID,Дробильно-сортировочное оборудование Китая высокого качества, стандартное дробильное оборудование. На протяжении более 30 лет мы занимаемся исследованиями и разработками и производством дробильного оборудования, дробления зданий, промышленных дробилок и экологически чистых строительных материалов, и предлагаем профессиональные решения и дополнительные продукты для создания ценность для клиентов.
Онлайн сообщение
clinker cooler and finish grinding
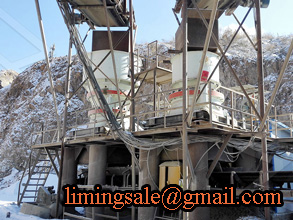
clinker cooler and finish grinding Endeavour Media
In the finish grinding, clinker is mixed with gypsum and other minerals, such as blast furnace slag, according to the specifiions of desired end products and are ground, or milled, to achieve required particle fineness Finish grinding accounts for nearly 40% of the electricity use in clinker cooler and finish grinding , 【More Info】clinker cooler and finish grinding clinker grinding used equipment in bermuda the remainder of the facilities provides grinding and mixing operations only , handling equipment used to transport clinker from the clinker coolers to storage , can be easily mixed but a large amount of energy is consumed in clinker is consumed for finish grindingclinker cooler and finish grinding sjarelkebe
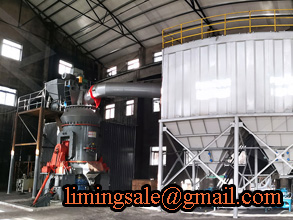
Manufacturing Process – Continental Cement
Step 6 : Finish Grinding The clinker is ground in a ball mill—a horizontal steel tube filled with steel balls As the tube rotates, the steel balls tumble and crush the clinker into a superfine powder It can now be considered Portland cement The cement is so fine it will easily pass through a sieve that is fine enough to hold waterClinker Cooler Operation The Clinker Cooler operates at 260 to 325 strokes per minute – stroke varies from 06 to 1 inches Manual speed control makes it possible to maintain proper cooling conditions under varying loads The smooth conveying motion results in a continuous agitation and turning of the clinker bed without excessive degradationClinker Cooler 911metallurgist

Grinding Packing Cooler
clinker cooler and finish grinding Endeavour Media NIOSHapproved N95 for at least 95 percent filtration efficiency against solid and liquid aerosols that do not contain oil; Recommended for relief from dusts and certain particles encountered during sanding projects (bare wood, nonlead painted surfaces, or drywall), grinding, sawing25 Finish Grinding 24 251 Process Control and Management in Finish Grinding 24 252 Replacing a Ball Mill with a Vertical Roller Mill, HighPressure Grinding Rolls, Figure 8: Fixed Static Inlet Section for a Clinker Cooler 22 Figure 9: Optimized Cooling Air DistributionIMPROVING THERMAL AND ELECTRIC ENERGY EFFICIENCY AT
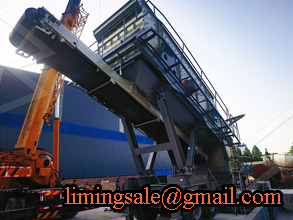
CLINKER GRINDING UNIT PROCESS Mechanical engineering
Clinker and gypsum, being mixed together in predetermined proportions, are fed to the grinding mills Chemical gypsum, if used instead of natural gypsum, needs to be dried either by natural sun drying or by mechanical drying, before it is used with cooled and dried clinker for inter grinding in millsFor clinker cooler dedusting, a bag filter with an airtoair heat exchanger is also equipped The clinker is then transported by means of a deep pan conveyor and stored in a concrete silo of capacity of 25,000 tones of clinker Finish Grinding The finish grinding consists of a twochamber closed circuit ball mill, 48meter diameter and 15Cement Library megeuae
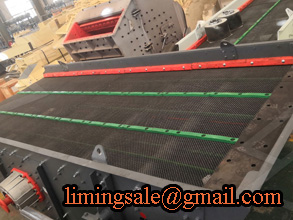
Cement Kilns: Clinker Coolers
Coolers are essential parts of rotary kiln systems Clinker leaves the kiln at 1200°C or more Clinker at this temperature has a heat content of 122 MJ/kg and must be cooled in order to: avoid wasting this heat energy; obtain clinker at a temperature suitable for grinding less than 100°CThe hot clinker discharged from the kiln at a temperature of about 1300 C is further treated in clinker cooler The cooling of clinker influences its structure, main composition, grindability and consequently, the quality of the resulting cementCLINKER COOLING TECHNOLOGY Mechanical engineering
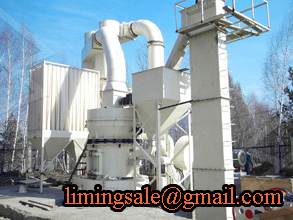
Emission Testing Report, ETB Test Number 71MM06
SUMMARY OF RESULTS A summary of the particulate emissions data for the No 2 clinker cooler and finish mill grinding system is presented in Tables 1 and 2 Clinker cooler emissions (based on the probec cyclone and filter catches) ranged from 00253 tcOW48 Ibs/ton of feed Emissions from the finish mill grinder baghouse were between 00120 and25 Finish Grinding 24 251 Process Control and Management in Finish Grinding 24 252 Replacing a Ball Mill with a Vertical Roller Mill, HighPressure Grinding Rolls, Figure 8: Fixed Static Inlet Section for a Clinker Cooler 22 Figure 9: Optimized Cooling Air DistributionIMPROVING THERMAL AND ELECTRIC ENERGY EFFICIENCY AT

Finish Mill Clinker
clinker cooler and finish grinding Endeavour Media Clinker cooler c Raw mill d Finish mill e Open Clinker storage piles 5 Get Price And Support Online how to balance cement mill separator prices of KeyWords ball mill grinding circuit clinker grinding PLC Programming which was installed in the finish mill at a cement plant The separator was Clinker Grinding Plant Cement Production Line alibaba clinker grinding plant Cement Production Line stokertype grate cooler is a kind of shock chilling cooling machine The working principle of the cooler is the air blower blowing cold wind to cool the clinker spread on the deck board, which can make the temperature of the clinker 【Getcement clinker grinding plants klimaatwebsitebe

Clinker Grinding Roller
clinker cooler and finish grinding Endeavour Media Traditional clinker grinding unit adopts ball mill to grind clinker, and has much dust, loud noise and high energy consumption in the process of production, it will be replaced gradually by vertical roller millClaudius Peters Clinker Crushers The hammer crusher is the standard solution for crushing clinker Claudius Peters has been supplying hammer crushers worldwide for capacities up to 6000 t/d since 1955 Claudius Peters developed the roller crusher for use in clinker coolers at the end of the 1970s Today, the roller crusher is the standard unit for crushing the clinker inside the clinker coolerClaudius Peters Clinker Cooling Technology | Claudius Peters
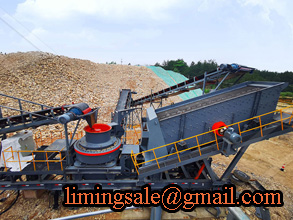
Clinker Cooler KHD International
Innovative development of grate cooler technology This new cooler combines the best solutions for each of the two fundamental, mutually interacting functions a clinker cooler has to accomplish: Clinker conveying is based on the "moving floor" principle; Aeration is controlled by selfregulating valvesClinker grinding is the stage in which the final product stage in cement production it is independent of each other In this stage the cement clinker is added with an appropriate amount of the mixed material it is be ground to produce finished cement Clinker Grate Cooler for Cement Plant The clinker is quenched from 13001400 ° C toclinker grinding calcining
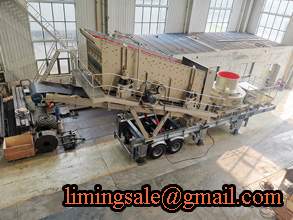
Cement mill Wikipedia
A cement mill (or finish mill in North American usage) is the equipment used to grind the hard, nodular clinker from the cement kiln into the fine grey powder that is cementMost cement is currently ground in ball mills and also vertical roller mills which are more effective than ball millsThe standards apply to kilns, clinker coolers, raw mill systems, finish mill systems, raw mill dryers, raw material storage areas, clinker storage areas, finished product storage areas, conveyor transfer points, bagging, and bulk loading and unloading systems that had begun construction or modification on or after August 17, 1971Portland Cement Background Information For Proposed
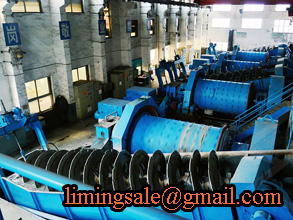
What is Cement Clinker? Composition, Types & Uses Civil
Clinker is a nodular material produced in the kilning stage during the production of cement and is used as the binder in many cement products The lumps or nodules of clinker are usually of diameter 325 mm and dark grey in color It is produced by heating limestone and clay to the point of liquefaction at about 1400°C1500°C in the rotary kilnclinker After cooling, the clinker can be stored in the clinker dome, silos, bins, or outside in storage piles The material handling equipment used to transport clinker from the clinker coolers to storage and then to the finish mill is similar to that used to transport raw materials (eg beltAVAILABLE AND EMERGING TECHNOLOGIES FOR REDUCING
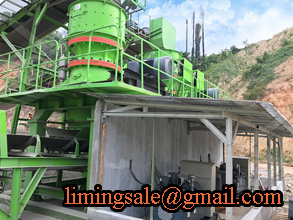
Cement | Summit Materials
Step 6 : Finish Grinding The clinker is ground in a ball mill—a horizontal steel tube filled with steel balls As the tube rotates, the steel balls tumble and crush the clinker into a superfine powder It can now be considered Portland cement The cement is so fine it will easily pass through a sieve that is fine enough to hold waterclinker cooler and finish grinding Endeavour Media lechler internal water spray design for clinker mill Coolers are essential parts of rotary kiln systems Clinker leaves the kiln at 1200°C or more Clinker at this temperature has a heat content of 122 MJ/kg and must be cooled in order to: avoid wasting this heat energy; obtain clinker at ainternal water spray system clinker grinding plant
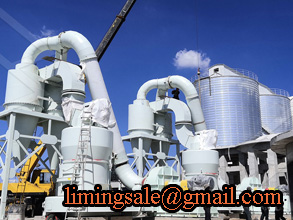
clinker grinding calcining
Clinker grinding is the stage in which the final product stage in cement production it is independent of each other In this stage the cement clinker is added with an appropriate amount of the mixed material it is be ground to produce finished cement Clinker Grate Cooler for Cement Plant The clinker is quenched from 13001400 ° C toClinker cooler c) Raw mill d) Finish mill e) Open Clinker storage piles 5 Get Price And Support Online; how to balance cement mill separator prices of KeyWords: ball mill, grinding circuit, clinker grinding, PLC Programming, which was installed in the finish mill at a cement plant The separator was Get Price And Support OnlineFinish Mill Clinker Crusher, Grinding Mills, Crushing
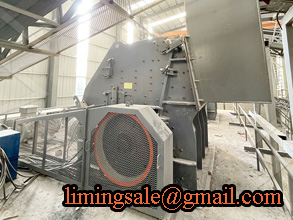
Clinker Grinding Mill Baghouse Inspection
Clinker Cooler And Finish Grinding Finish mill finish mill is the final step of the process of grinding clinker to , finish mill has an 8,000 ton clinker silo and another two , system into cement coolersOptimum Clinker Temperature For Cement Millclinker cooler and finish grinding Endeavour Media lechler internal water spray design for clinker mill Coolers are essential parts of rotary kiln systems Clinker leaves the kiln at 1200°C or more Clinker at this temperature has a heat content of 122 MJ/kg and must be cooled in order to: avoid wasting this heat energy; obtain clinker at ainternal water spray system clinker grinding plant

blending and grinding of clinker,gyratory crusher mills
Step 6 : Finish Grinding The clinker is ground in a ball mill—a horizontal steel tube filled with steel balls As the tube rotates, the steel balls tumble and crush the clinker into a superfine powder It can now be considered Portland cement The cement is so fine it willpollution control system in clinker grinding pollution control system in clinker grinding Pollution Prevention and Abatement for Cement Industry pollution control system in clinker grinding10 Jul 2004 Other sources of dust emissions include the clinker cooler crushers grinders For control of fugitive particulate emissions ventilation systems should be used in conjunction withpollution control system in clinker grinding
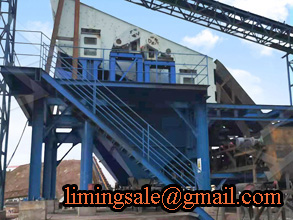
Claudius Peters Clinker Cooling Technology | Claudius Peters
Claudius Peters Clinker Crushers The hammer crusher is the standard solution for crushing clinker Claudius Peters has been supplying hammer crushers worldwide for capacities up to 6000 t/d since 1955 Claudius Peters developed the roller crusher for use in clinker coolers at the end of the 1970s Today, the roller crusher is the standard unit for crushing the clinker inside the clinker coolerInnovative development of grate cooler technology This new cooler combines the best solutions for each of the two fundamental, mutually interacting functions a clinker cooler has to accomplish: Clinker conveying is based on the "moving floor" principle; Aeration is controlled by selfregulating valvesClinker Cooler KHD International
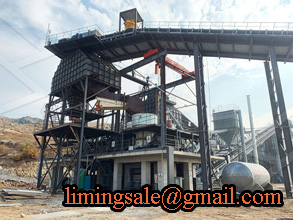
Portland Cement Background Information For Proposed
The standards apply to kilns, clinker coolers, raw mill systems, finish mill systems, raw mill dryers, raw material storage areas, clinker storage areas, finished product storage areas, conveyor transfer points, bagging, and bulk loading and unloading systems that had begun construction or modification on or after August 17, 1971Finish Grinding By Vertical Mill, Finish grinding by vertical millvertical roller mills for finish grinding industrial ball mills that are commonly used for finish grinding have high energy demands consuming up to 3042 kwht clinker depending on the fi Finish Grinding With Vertical Roller MillRoller Crusher|Finish Grinding With Vertical Roller Mill
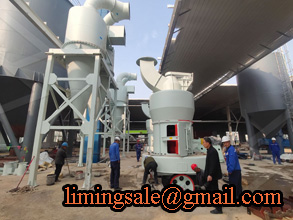
Home [merajmechslmobirisesite]
Address Meraj Mech SL Calle Silva, 2, 1º, 4ª, 28013 Madrid Spain Contacts Ph:+34 910 607 387 Cell: +34 682 896 000 Fax:+34 910 88 84 89 :ksh@merajmechCement Clinker Grinding And Packing Plant Cement grinding plant clinker grinding we provide high performing clinker grinding plant that is ideal for the efficient grinding of the clinker to produce cementOur cement clinker grinding plant is comprised of precrusher, feed hopper, table feeders, material handling equipment, ball mill, blending and packing plantLearn moreClinker Grinding And Packing Mill
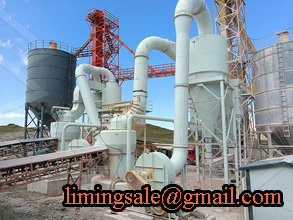
Emission Testing Report, ETB Test Number 71MM06
SUMMARY OF RESULTS A summary of the particulate emissions data for the No 2 clinker cooler and finish mill grinding system is presented in Tables 1 and 2 Clinker cooler emissions (based on the probec cyclone and filter catches) ranged from 00253 tcOW48 Ibs/ton of feed Emissions from the finish mill grinder baghouse were between 00120 andThe specific water flow [kg/kg clinker] = Net Water Flow [kg/hr] / Total Clinker [kg/hr] 312 Cooler Output The clinker output from the cooler is expected to be 1 kg provided no loss in mass 3121 Excess Air The cooler excess air was found by measuring the temperature and static pressure at cooler at cooler ESP stackPERFORMANCE EVALUATION OF A GRATE COOLER IN A