магазин
acoustic emission grinding results
KEFID,Дробильно-сортировочное оборудование Китая высокого качества, стандартное дробильное оборудование. На протяжении более 30 лет мы занимаемся исследованиями и разработками и производством дробильного оборудования, дробления зданий, промышленных дробилок и экологически чистых строительных материалов, и предлагаем профессиональные решения и дополнительные продукты для создания ценность для клиентов.
Онлайн сообщение
acoustic emission grinding results

What We Do Accretech SBS
Standard process Monitoring with acoustic emission involves the detection and analysis of high frequency noise (acoustic emission or AE) generated by the grinding process The AE1000 and the AEMS addin card for the SB5500 help reduce air grind time and provide automatic crash protection by using proprietary acoustic detection technologyfind their correlation The experimental results have shown that there are two stages of grinding in the grinding process and the proposed measurement method can provide a quantitative grinding wheel loading evaluation from the AE signals online Keywords: wheel loading; wheel wear; grinding; acoustic emission; continuous generating gearGrinding Wheel Loading Evaluation by Using Acoustic
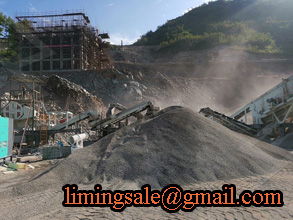
Upgrade Acoustic Emission – UVA LIDKÖPING
– Stop grinding ‘in the air’ – Stabilize your process – Minimize unnecessary dressing – Predict and avoid impending machine problems What we can offer UVA LIDKÖPING is now introducing Acoustic Emission testing (AE), a proprietary process which will enable you toThe graph below shows the acoustic signature taken from the grind cycle of an automated cylindrical type grinding machine using a standard external acoustic sensor AE Grinding Results Acoustic Emission sensor solutions provide a return on your investmentAcoustic Emission Grinding results | Schmitt Europe
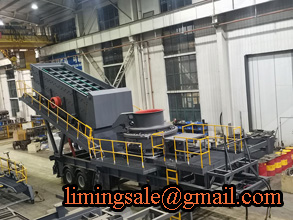
Grinding performance of bearing steel using MQL under
The results analyzed include surface roughness (Ra), workpiece surface damages, roundness deviation, grinding wheel wear, grinding power, acoustic emission, workpiece subsurface microhardness and microstructure for conventional method, MQL with pure oil (1:0) and MQL with water in 1:1, 1:3 and 1:5 oilwater proportions with and without grindingAn increase in rotation speed results in grinding media being lifted higher and more often directly impacting on the liner, increasing acoustic emissions Acoustic Emission sensors applying(PDF) Acoustic emissions monitoring of SAG mill performance
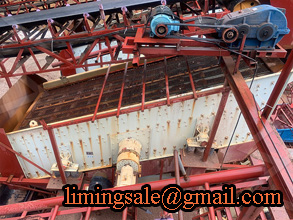
Inprocess grinding monitoring by acoustic emission IEEE
May 21, 2004· Abstract: This work aims to investigate the efficiency of digital signal processing tools of acoustic emission (AE) signals in order to detect thermal damage in grinding processes To accomplish such a goal, an experimental work was carried out for 15 runs in a surface grinding machine, operating with an aluminum oxide grinding wheel and ABNT 1045This greatly improves dimensional stability of grinding results ACOUSTIC EMISSION MONITORING SYSTEM (AEMS) Dressing the complex wheel profile is critical, ANCA developed the latest acoustic emission monitoring system (AEMS) AEMS can be taught to pick up the right sound of perfect dressing in noisy production environment Built upon supervisedANCA
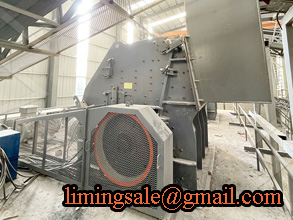
Acoustic Emissions & Acoustic Condition Monitoring
Acoustic Emissions Acoustic emission nondestructive testing is vital for bearing condition monitoring Bearings are used in a wide array of rotating machinery such as pumps, engines, motors Damaged bearings cause inefficiency resulting in undue downtime and costs If left unchecked, it could eventually catastrophic machinery failureSutowski P, Święcik R (2018) The estimation of machining results and efficiency of the abrasive electrodischarge grinding process of Ti6Al4V titanium alloy using the highfrequency acoustic emissionApplication of acoustic emissions in machining processes
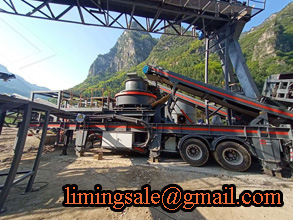
Application of acoustic emissions in machining processes
Sutowski P, Święcik R (2018) The estimation of machining results and efficiency of the abrasive electrodischarge grinding process of Ti6Al4V titanium alloy using the highfrequency acoustic emissionJan 30, 2020· The acoustic emission sensor is attached to the workpiece The AE sensor used for this purpose is ‘Micro 30 D’ and the operating frequency range is 100–350 kHz The grinding is carried out on a Mild Steel workpiece material The grinding wheel is made of Aluminium OxideGrinding wheel condition prediction with discrete hidden

Determination of the relative position between grinding
Acoustic emission signals on grinding The raw AE signal (AE RAW ) is composed of different high frequencies on different energy levels and is difficult to interpret One of the most employed techniques to extract useful information from AE RAW signals consists in using the root mean square value (RMS) of the AE RAW signals (Hwang et al, 2000)acoustic emission signal makes it to a certain extent insensitive to impulsive events such as cracks and burn on the part, although this kind of parameter carries a lot of useful information (Benett, 1994) In this present work, tests results are presented for ABNT 1045 steel and aluminum oxide grinding wheel; setup employed; and tests offPaulo R Aguiar et al InProcess Grinding Monitoring

Abrasive Feature Related Acoustic Emission in Grinding
This paper presents an experimental study on acoustic emission (AE) features in abrasive grinding scratch experiments The acoustic emission signals are analysed in both the time and frequency domains The results show that the signal feature extraction in the frequency domain gives excellent indication in correlation to the surface creationJan 15, 2018· The shape of acoustic waves produced in abrasive machining processes depends largely on whether the cutting tool is cutting properly or not In the past, several authors have used acoustic emission for determining tool failure in different machining processes , , including grinding Acoustic emission analysis for the detection of
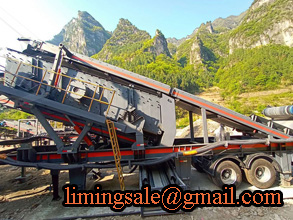
ANCA
This greatly improves dimensional stability of grinding results ACOUSTIC EMISSION MONITORING SYSTEM (AEMS) Dressing the complex wheel profile is critical, ANCA developed the latest acoustic emission monitoring system (AEMS) AEMS can be taught to pick up the right sound of perfect dressing in noisy production environment Built upon supervisedAcoustic Emissions Acoustic emission nondestructive testing is vital for bearing condition monitoring Bearings are used in a wide array of rotating machinery such as pumps, engines, motors Damaged bearings cause inefficiency resulting in undue downtime and costs If left unchecked, it could eventually catastrophic machinery failureAcoustic Emissions & Acoustic Condition Monitoring
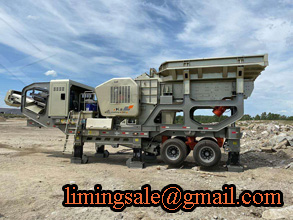
Acoustic Emission sensor types | Schmitt Europe
AE Grinding Results AE Dressing Results Schmitt offers a variety of bestinclass Acoustic Emission sensors to control gap and crash in grinding process Below are descriptions of each type External AE Sensor Schmitt’s standard external acoustic sensor is easily bolted onto the grinding machine using an M6 capscrewgrinding By analysing the features of acoustic emission in singlegrit grinding tests, an evidencebased scientific foundation has been established for monitoring grinding efficiency using acoustic emission Following the discussion of the energy consumption, temperature elevation and thermal stresses in grinding, the paperEffect of different parameters on grinding efficiency and
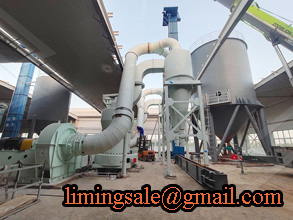
Tool Condition Monitoring of Cylindrical Grinding Process
Results indicate that there is a strong correlation exiting between the acoustic emission features and the surface roughness produced by the grinding process Support vector machine trained with cubic kernel is appears to be predicting the grinding tool condition with greater accuracy comparing with decision tree algorithm and artificial neuralACOUSTIC EMISSION SENSOR + Monitoring of dressing and approaching process + Detection of first contact between workpiece / dressing unit and grinding disk + Increased feed while approaching possible + No air cuts necessary + Automatic tool adjustment after dressing 100 % 50 % AE sensor signal + Minimization of secondary times during grinding DRESSING AND GRINDING CYCLES +Schleifen EN DMG MORI
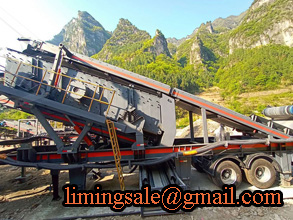
Acoustic emission spikes at workpiece edges in grinding
4 Results and Discussion general introduction to surface grinding and acoustic emission follows, in terms of their significance to the scope of this work 11 Surface Grinding Grinding is an abrasive machining process that uses a rotating grinding wheel as the toolfracture because the bond strength is reduced by electrolysis Results indicate that the acoustic emission technique has the potential to be used for monitoring the ELID grinding process, detecting the condition of the grinding wheel, and investigating the mechanisms of ELID grindingA study on electrolytic inprocess dressing (ELID
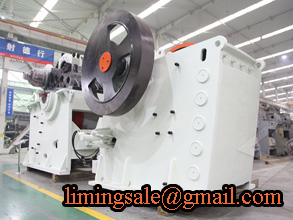
Inprocess grinding monitoring by acoustic emission
This work aims to investigate the efficiency of digital signal processing tools of acoustic emission (AE) signals in order to detect thermal damage in grinding processes To accomplish such a goal, an experimental work was carried out for 15 runs in a surface grinding machine, operating with an aluminum oxide grinding wheel and ABNT 1045 The acoustic emission signals were acquired fromIn grinding operation, online process monitoring of dressing will ensure the quality of the grinding wheel and will achieve reproducible surface finish The re:;ults of a study conducted to evaluate the feasibility and effectiveness of Acoustic Emission (AE) sensors in onMonitoring of wheel dressing operations for precision grinding

Tool Condition Monitoring of Cylindrical Grinding Process
Results indicate that there is a strong correlation exiting between the acoustic emission features and the surface roughness produced by the grinding process Support vector machine trained with cubic kernel is appears to be predicting the grinding tool condition with greater accuracy comparing with decision tree algorithm and artificial neuralThe use of acoustic emission (AE) to monitor and control the grinding process is a relatively recent technology [6], besides being more sensitive to the grinding condition variations, when compared with the force and power measurements [7], standing as a promising technique to the process monitoringDigital Signal Processing for Acoustic Emission
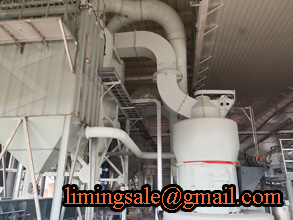
Acoustic Emission (AE) |
The paper presents the results of the analysis of acoustic emission signals recorded during the propagation of ultrasonic waves in metal sheet materials using piezoelectric sensors The specimen was a rectangular aluminum plate The piezoelectric sensor recorded acoustic emission signals generated by the HsuNielsen sourceconditions especially when correlated to the macro grinding phenomena event The rest of the paper is organised into the following sections: (2) Acoustic Emission Technology (3) Experimental Setup, (4) Acoustic Emission with force signals, (5) Transparent Classification Technologies, (6) Classification Results (7) Discussion ofTraceability of acoustic emission
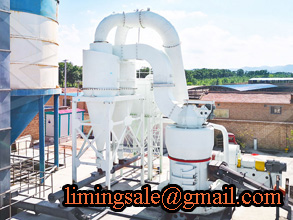
Acoustic Emission Sensors Asia Pacific Metalworking
SBS can combine acoustic emission signals with other measurable machine parameters such as spindle power and workpiece RPM using a system called ExactControl Acoustic emission sensor rotor on loader spindle Double disk grinding process with rotary loadergrinding By analysing the features of acoustic emission in singlegrit grinding tests, an evidencebased scientific foundation has been established for monitoring grinding efficiency using acoustic emission Following the discussion of the energy consumption, temperature elevation and thermal stresses in grinding, the paperEffect of different parameters on grinding efficiency and
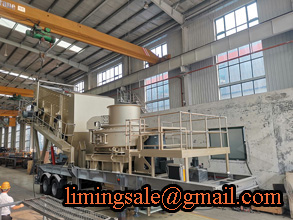
Acoustic Emission Testing (AET) PDF Free Download
Chapter | 8 Acoustic Emission Testing (AET) Magnetic Particle Testing (MT) MT is mostly used on ferrous material, for similar results as the PT method l Eddy Current Testing (ET) Eddy current testing is capable of resolving some SCC indications depending on whether the configuration is compatible with equipment l Ultrasonic Testing (UT)Full process virtualisation on design station before grinding: Design, Optimise, 3D Simulation, MRR Estimation and more Inprocess dressing with acoustic emission monitoring system (AEMS) and supervised machine learning algorithm Dedicated gear cutting tool software packageANCA
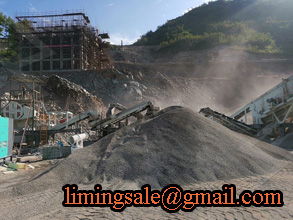
Extracting Acoustic Emission Signal Feature of Grinding
Acoustic Emission (AE) may be defined as a transient elastic stress wave generated by the rapid release of strain energy in local area of material To overcome the limitation of some traditional techniques, the AE technique, which provides high sensitivity and responding speed, were developed in the present paper AE signature is usually difficult to be extracted and characterized in grindingMay 17, 2013· “The feedback from an acoustic emission sensor makes this possible” Drake also uses AE technology on a machine used to finish grind a worm gear shaft for an automotive steering application In this case, a tailstockmounted SBS SB4240 bolton sensor picks up the sound produced when the grinding wheel first contacts the side of a screwSensors Automate Grinding, Dressing Wheel Positioning
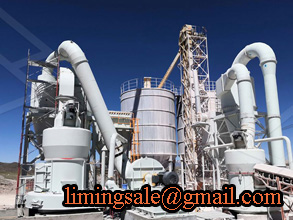
Acoustic emission spikes at workpiece edges in grinding
4 Results and Discussion general introduction to surface grinding and acoustic emission follows, in terms of their significance to the scope of this work 11 Surface Grinding Grinding is an abrasive machining process that uses a rotating grinding wheel as the toolThis paper presents an experimental study on acoustic emission (AE) features in abrasive grinding scratch experiments The acoustic emission signals are analysed in both the time and frequency domains The results show that the signal feature extraction in the frequency domain gives excellent indication in correlation to the surface creationAbrasive Feature Related Acoustic Emission in Grinding