магазин
flue gas for coal dryer
KEFID,Дробильно-сортировочное оборудование Китая высокого качества, стандартное дробильное оборудование. На протяжении более 30 лет мы занимаемся исследованиями и разработками и производством дробильного оборудования, дробления зданий, промышленных дробилок и экологически чистых строительных материалов, и предлагаем профессиональные решения и дополнительные продукты для создания ценность для клиентов.
Онлайн сообщение
flue gas for coal dryer
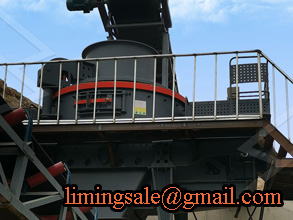
Coal Dryer Kilburn
The exhaust gas from the dryer is passed through a bag filter for removing the fines carried over before releasing it to the atmosphere It is also possible to recirculate part of the flue gas from bag filter outlet to dryer This minimizes chances of explosion by reducing oxygen content in flue gasJun 30, 2007· With the fullscale coaldrying system operating at the target moisture reduction level, the flue gas flow rate to the spray towers will be reduced by about 4%, further lowering SO 2 emissionsLignite Drying: New CoalDrying Technology Promises Higher
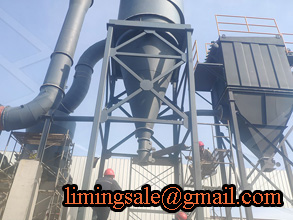
Coal Drying Improves Performance and Reduces Emissions
The flow rate of flue gas leaving the furnace firing drier coal is lower compared to the wet fuel Also, the specific heat of the flue gas is lower due to the lower moisture content The result is reduced thermal energy of the flue gas Lower flue gas flow rate also results in lower rates of convective heat transferThe coal dryer works on the principle of agitated fluid bed coal drying The coal dryer removes the moisture from the unsized coal available at power stations as well as for process boilers The hot air required for coal dryer is generated from burning the coal fines dried in the coal dryer Superior Features Handles coal lumps of 40 to 200 mmCoal Dryer Manufacturer, India TTPL
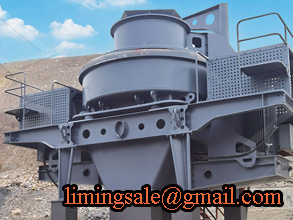
Impact of solid waste treatment from spray dryer absorber
Management of solid wastes from coalfired power plants • Semidry flue gas desulfurization solids contain calcium sulfite • Dry oxidation of calcium sulfite in fluidized bed reactor • Treated semidry flue gas desulfurization waste use as classC flyash and cement kiln feed • Impact on levelized cost of energy is shown to be smallwith the real process, the composition of the flue gas generated in the laboratory will have to be close to that of the flue gas resulting from a coalfired boiler The flue gas, after leaving the combustion chamber, enter a heat exchanger, with the role of lowering their temperature down to the value required at the dryer inletCOAL DRYING IN FLUIDIZED BED USING FLUE GAS
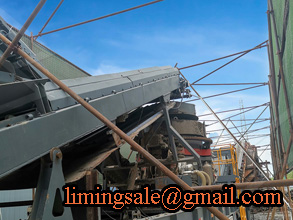
The economic solution for Flue Gas Desulphurisation
Large SDA’s clean the flue gas from a 550 MW e coal fired power plant in the USA Two parallel absorber modules treat the flue gas from 8 lignite fired boilers installed in the Czech Rep 530 MW e lignite fired power plant in the Czech Rep • Mixing tank with agitator, heating jacket and lid with gasSep 14, 2015· Each boiler uses a single SDA followed by a pulse jet fabric filter to treat the flue gas produced by the pet coke and coalfired unit SO 2 emissions are reduced up toCirculating Fluidized Bed Scrubber vs Spray Dryer
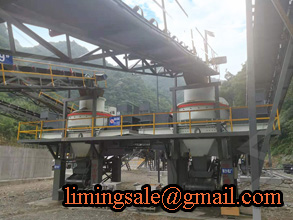
Coal Dryer Manufacturer, India TTPL
The coal dryer works on the principle of agitated fluid bed coal drying The coal dryer removes the moisture from the unsized coal available at power stations as well as for process boilers The hot air required for coal dryer is generated from burning the coal fines dried in the coal dryer Superior Features Handles coal lumps of 40 to 200 mmwith the real process, the composition of the flue gas generated in the laboratory will have to be close to that of the flue gas resulting from a coalfired boiler The flue gas, after leaving the combustion chamber, enter a heat exchanger, with the role of lowering their temperature down to the value required at the dryer inletCOAL DRYING IN FLUIDIZED BED USING FLUE GAS
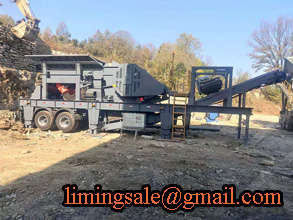
Design of advanced fossil fuel systems (DAFFS): a study of
Abstract The objectives of this report are to present: the facility description, plant layouts and additional information which define the conceptual engineering design, performance and cost estimates for the pulverized coal fired (PCF) power plant which utilizes highsulfur coal as fuel, and a spray dryer/fabric filter flue gas desulfurization (FGD) system; an assessment of the impact ofManagement of solid wastes from coalfired power plants • Semidry flue gas desulfurization solids contain calcium sulfite • Dry oxidation of calcium sulfite in fluidized bed reactor • Treated semidry flue gas desulfurization waste use as classC flyash and cement kiln feed • Impact on levelized cost of energy is shown to be smallImpact of solid waste treatment from spray dryer absorber
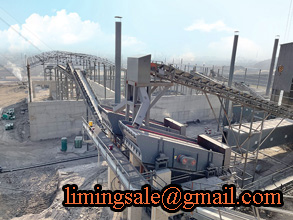
Spray Dryer Absorber GEA engineering for a better world
Hot, untreated flue gas is introduced into the Spray Dryer Absorber via a flue gas disperser and subsequently comes into contact with a highly reactive absorbent that will be atomized by a Rotary Atomizer An efficient contact between flue gas and absorbent allows for rapid mass transfer of acidic components from the flue gas into the alkalineTTPL is one of the best dryer manufacturer in india We are manufacturers flash dryer, spray dryer, fly ash dryer, pond ash dryer, coal dryer, fluid bed dryer, spray cooler, bulk flow cooler in pune india The company started its business by offering customized and energy efficient dryers, such as spray dryers & flash dryersFlash/Spray/Coal Dryer, Fly/Pond Ash Dryer, Spray/Bulk
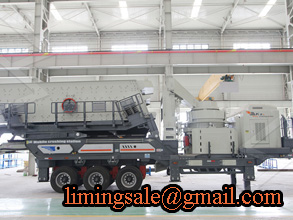
Flue Gas Desulfurization (FGD) NolTec
RK Srivastava and W Jozewicz, “Flue Gas Desulfurization: The State of the Art,” Journal of the Air & Waste Management Association, vol 51, p 16761688, December 2001 Dry Hydrated Lime Injection for CoalFired Boiler (FGD) (PDF)Flue Gas Desulfurization and Acid Gas ControlFlue Gas Desulfurization and Acid Gas Control Spray Dry FGD • Up to 95% SO 2 removal • Lower sulfur fuels Spray Dry FGD • Typically <15% sulfur coal System • Up to 98+% SO 2 removal 15% sulfur coal • Dry product for landfill • Uses lime to 98+% SO • High sulfur fuels (>15%) • MoreWorldwide Pollution Control Association

Indirect rotary dryers | IDRECO Srl
The hot flue gas at the annular furnace exit are conveyed to a Air Preheater, for heating combustion air and reduce tail gas consumption, and finally are discharged to the atmosphere through a stack Indirect Flue Gas Tube Dryer Another type of indirect rotary dryer is the flue gas tube typeFlue gas is the gas exiting to the atmosphere via a flue, which is a pipe or channel for conveying exhaust gases from a fireplace, oven, furnace, boiler or steam generatorQuite often, the flue gas refers to the combustion exhaust gas produced at power plantsIts composition depends on what is being burned, but it will usually consist of mostly nitrogen (typically more than twothirds) derivedFlue gas Wikipedia
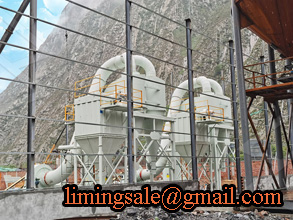
Flue gas desulfurization idconline
Oct 21, 1974· Spraydryers are used upstream of the particulate removal equipment (electrical precipitator or filter baghouse) where the flue gas contains the combustion fly ash In a spraydryer system, the alkaline sorbent is usually lime slurry The slurry is atomized and sprayed into a vessel as a cloud of fine bubbles where it contacts the hot flue gasthe 8inch diameter flue gas duct upstream of the spray dryer, entered the spray dryer with the flue gas and passed through the concentric inlet vanes which surrounded the atomizer and was therefore distributed uniformly into the spray dryer with the flue gas The gaseous ammonia was supplied from a liquid NH3 holding tank TheA Combined Ca(OH)2/NH3 Flue Gas Desulfurization Process

Spray Dryer Components Flue Gas Desulfurization (FGD
Flue Gas Desulfurization RPM Solutions, Inc specializes in building and maintaining Flue Gas Desulfurization (FGD) components FGD systems remove sulfur dioxide (SO2) from the exhaust of flue gases in electric power plants that burn coal or oil RPM Solutions components are specifically designed for dry sorbent injection systems (DSI), or dryAn experimental study of spray dryer flue gas desulfurization has been carried out with the objective of evaluating this technology for potential use in facilities burning Eastern US coals The investigation was conducted using a 500 lb/hr pulverizedcoalfired furnace equipped with a spray dryer and baghouseDry flue gas desulfurization process for various coals
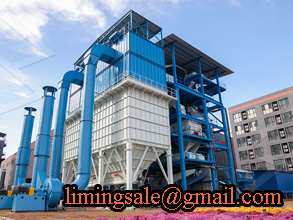
CNA Flue gas low temperature denitriding and
The invention discloses a flue gas low temperature denitriding and coal slime drying combined circulating system, which comprises a boiler, wherein the hearth outlet of the boiler is connected with a chimney through an flue gas exhaust channel; an electrical deduster and a desulfurizer are arranged on the flue gas exhaust channel; a first pipe is arranged on the flue gas exhaust channelThe Exergy Flue Gas Dryer was developed to meet the needs of the industry for the utilisation of latent heat in flue gases from boilers The dryer consists of feeding and discharge equipment, a separation cyclone and specially designed drying conduits The biomass is fed in hot flues gas stream and gets in direct contact with flues gasesFlue Gas Dryer | Industrial Dryers | Swedish Exergy
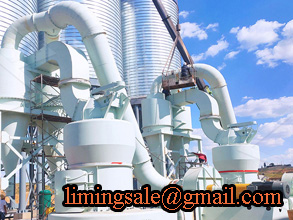
How to deal with the flue gas of the charcoal machine?
Charcoal production line which links need to set up smoke removal equipment? Generally, in the charcoal production line, the charcoal furnace (including the selfbuilt charcoal kiln), dryer machine and sawdust briquette machine and other production links are required to set up smoke and dust removal equipment Flue gas recovery and purification system are specially used for charcoal productionHot, untreated flue gas is introduced into the Spray Dryer Absorber via a flue gas disperser and subsequently comes into contact with a highly reactive absorbent that will be atomized by a Rotary Atomizer An efficient contact between flue gas and absorbent allows for rapid mass transfer of acidic components from the flue gas into the alkalineSpray Dryer Absorber GEA engineering for a better world
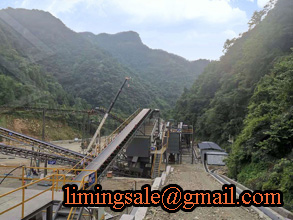
Flue Gas Desulfurization System India, Flue Gas
Flue Gas Desulphurization Technology Selection Criteria The selection of flue gas desulphurization technology (FGD) is done on the basis of economic, technical and commercial aspects These include capital cost, operating cost, the efficiency to remove SO2, performance reliability, space requirement, and a proven track recordTTPL is one of the best dryer manufacturer in india We are manufacturers flash dryer, spray dryer, fly ash dryer, pond ash dryer, coal dryer, fluid bed dryer, spray cooler, bulk flow cooler in pune india The company started its business by offering customized and energy efficient dryers, such as spray dryers & flash dryersFlash/Spray/Coal Dryer, Fly/Pond Ash Dryer, Spray/Bulk
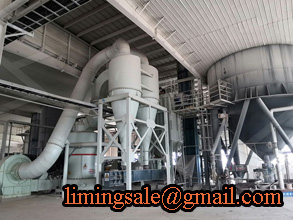
Pilotscale Parametric Testing Of Spray Dryer So2 Scrubber
Spray dryer flue gas residence time of 816 sec and spray dryer inlet S02 con centration of 1852150 ppm have very little effect on S02 removal Fabric Filter S02 Removal IThe process parameters that significantly affect fabric filter S02 removal are: stoichiometric ratio, ap proach to adiabatic saturation temper ature, and recycle ratioEPACICA Fact Sheet Flue Gas Desulfurization1 Name of Technology: Flue waste Nonetheless, it is the preferred process for coalfired electric utility power plants burning coal SemiDry Systems Semidry systems, or spray dryers, inject an aqueous sorbent slurry similar to a wet system, however, the slurry has a higher sorbentAir Pollution Control Technology Fact Sheet

Sulphur dioxide (SO2) emissions control Platte River
The SO2 emissions are controlled using a spray dryer absorber (SDA) flue gas desulfurization system During the SDA process, hot flue gas with entrained coal flyash passes through large reaction chambers where a mixture of recycled flyash/SDA product slurry, and limewater slurry (calcium hydroxide) is sprayed and atomizedAbstract The objectives of this report are to present: the facility description, plant layouts and additional information which define the conceptual engineering design, performance and cost estimates for the pulverized coal fired (PCF) power plant which utilizes highsulfur coal as fuel, and a spray dryer/fabric filter flue gas desulfurization (FGD) system; an assessment of the impact ofDesign of advanced fossil fuel systems (DAFFS): a study of
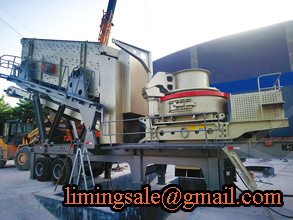
Indirect rotary dryers | IDRECO Srl
The hot flue gas at the annular furnace exit are conveyed to a Air Preheater, for heating combustion air and reduce tail gas consumption, and finally are discharged to the atmosphere through a stack Indirect Flue Gas Tube Dryer Another type of indirect rotary dryer is the flue gas tube type1 Introduction CO 2 is a greenhouse gas with a significant impact on climate change [] and a large amount of CO 2 is emitted to the environment by power plant flue gases It is very probable that, despite the high risk of global warming, the number of coalfired power plants in countries with large coal reserves, such as China and the United States of America, will increase in the future []Separation of Carbon Dioxide from Real Power Plant Flue