магазин
cement mills diagram
KEFID,Дробильно-сортировочное оборудование Китая высокого качества, стандартное дробильное оборудование. На протяжении более 30 лет мы занимаемся исследованиями и разработками и производством дробильного оборудования, дробления зданий, промышленных дробилок и экологически чистых строительных материалов, и предлагаем профессиональные решения и дополнительные продукты для создания ценность для клиентов.
Онлайн сообщение
cement mills diagram
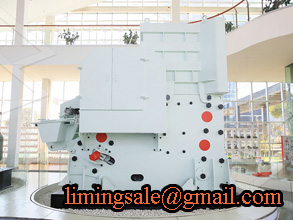
Cement Manufacturing Process | Phases | Flow Chart
Aug 30, 2012· Material is directly conveyed to the silos (silos are the large storage tanks of cement) from the grinding mills Further, it is packed to about 2040 kg bags Only a small percent of cement is packed in the bags only for those customers whom need is very small The remaining cement is shipped in bulk quantities by mean of trucks, rails or shipsGearless mill drives with the dry cement process In 1985, ABB delivered the first GMD for mineral processing at an ore mill at Bougainville, New Guinea Since then innovation has continued with the first GMD for a doublerotating ball mill in Carlin, Nevada, meeting a 160 °C heat challenge at the mill shell GMDs have now been supplied for the world'sdiagram of cement mill pdf gilhobbybe
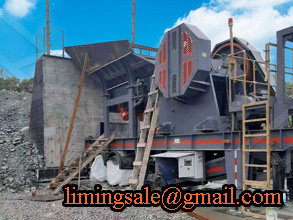
Cement Mill Motor Ht Motor Single Line Diagram Ball Mill
Westinghouse 350 hp 870 rpm electric motor jw site layout diagram and aggregate flow charts equipment finder westinghouse 350 hp 870 rpm electric motor category parts description description motor was used to power bowl mill in cement plant 3 phase 4000 volts 60 cycles 48 amps 6865 s frame nema c rating price 6500 get price moreDec 13, 2018· The flowsheet diagram of the wet process for manufacturing Portland cement is given in Figure 33 The limestone is disintegrated in crushers The crushed limestone is fed to tube mill, where the limestone and the clay, introduced as a slurry from aExplain dry and wet process of cement manufacturing
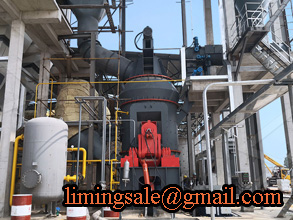
116 Portland Cement Manufacturing
Aug 17, 1971· materials are produced in portland cement manufacturing plants A diagram of the process, which encompasses production of both portland and masonry cement, is shown in Figure 1161 ball or tube mills, thereby producing a pumpable slurry, or slip, of approximately 65 percent solids The slurry is agitated, blended, and stored in variousadditive) are proportioned and ground in Cement mill (one Closed circuit ball mill in line 1 and two Roller press+closed circuit ball mill in line 2) based on the type of cement to be produced keeping the quality of cement equal or above the required standard For instance (Clinker+Pozzolana+Gypsum) are proportioned and milledCEMENT PRODUCTION AND QUALITY CONTROL A Cement
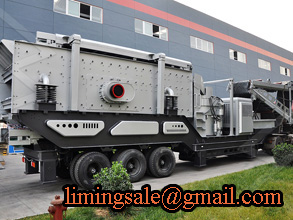
CHAPTER 30 CEMENT MANUFACTURING PROCESS
Flow Diagram of Cement Manufacturing Process then fed to the raw mill inlet with the help of belt conveyors Two types of Raw Mills are used for grinding raw material ie ball mill and vertical roller mill (VRM) The VRM combines the drying, grinding and separation processes into just one unitMar 15, 2017· Cement manufacturing process components of a cement plant from quarry to kiln to cement millCement Manufacturing Process Simplified Flow Chart
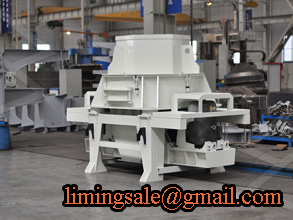
Explain dry and wet process of cement manufacturing
Dec 13, 2018· The flowsheet diagram of the wet process for manufacturing Portland cement is given in Figure 33 The limestone is disintegrated in crushers The crushed limestone is fed to tube mill, where the limestone and the clay, introduced as a slurry from aIn the diagram above of a precalciner kiln, raw meal passes down the preheater tower while hot gases rise up, heating the raw meal At 'A,' the raw meal largely decarbonates; at 'B,' the temperature is 1000 C 1200 C and intermediate compounds are forming and at 'C,' the burning zone, clinker nodules and the final clinker minerals formThe cement kiln

CHAPTER 30 CEMENT MANUFACTURING PROCESS
Flow Diagram of Cement Manufacturing Process then fed to the raw mill inlet with the help of belt conveyors Two types of Raw Mills are used for grinding raw material ie ball mill and vertical roller mill (VRM) The VRM combines the drying, grinding and separation processes into just one unitSep 17, 2015· The output of a cement mill is the final product viz Cement The term bag house is applied to large filters containing a number of tubular bags mounted in a usually rectangular casing The dust laden air is drawn through them by suction 14 15 Cement Storage Silo The cement storage silo is used for storing the finished product – cement 16Cement Production Process LinkedIn SlideShare
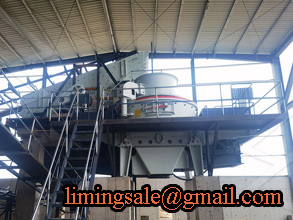
Online Course: Ball Mill cement grinding systems
Jun 24, 2015· 1 Safety around a ball mill 2 An overview of a ball mill 3 A ball mill’s components and the components’ functions, and on 4 Cement grinding systems with primary focus on closed circuitCEMENT MILL In cement process this is the final s tage The typical coal mill circuit diagram with temperature, pressure, oxygen percentage and flow of fans at various locations is (PDF) Energy audit of thermal utilities in a cement plant
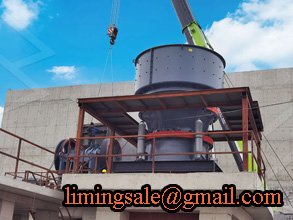
Cement Manufacturing Process: What is Cement made of
For cement packing, cloth, jute, and highdensity Polythene (HDPE) bags are commonly used For convenience, the cement comes to the customer in bags containing measured quantity The standard bag of cement as distributed in India is commonly 50 kg or 112 5 lbs 2 Wet Process of Manufacturing of Cementadditive) are proportioned and ground in Cement mill (one Closed circuit ball mill in line 1 and two Roller press+closed circuit ball mill in line 2) based on the type of cement to be produced keeping the quality of cement equal or above the required standard For instance (Clinker+Pozzolana+Gypsum) are proportioned and milledCEMENT PRODUCTION AND QUALITY CONTROL A Cement

Closed Circuit Grinding VS Open Circuit Grinding
Metallurgical ContentOpen Circuit GrindingClosed Circuit GrindingGrinding Circuit Process Control VariablesGrinding Operating Costs The simplest grinding circuit consists of a ball or rod mill in closed circuit with a classifier; the flow sheet is shown in Fig 25 and the actual layout in Fig 9 This singlestage circuit is chiefly employed for coarse grinding when a product finer than 65Cement manufacturing: components of a cement plant This page and the linked pages below summarize the cement manufacturing process from the perspective of the individual components of a cement plant the kiln, the cement mill etc For information on materials, including reactions in the kiln, see the ' Clinker ' pagesCement manufacturing components of a cement plant

loesche vertical roller mill hydraulic system flow diagram
vertical cement mill diagram – CGM Grinding Plant Sectional diagram of a FullcrLoesche vertical roller mill gas flow outside of a vertical mill; Diagram 5hydraulic systems for ball mills »More detailedDiagram of cement ball mill (Based on an image from ThyssenKrupp AG 15) Much of the energy consumed by a ball mill generates heat Water is injected into the second chamber of the mill to provide evaporative cooling Air flow through the mill is one medium for cement transport but also removes water vapour and makes some contribution to coolingBall Mills an overview | ScienceDirect Topics
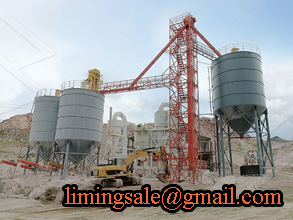
ES Processing | Advanced Process Control and Process
ES Processing is a leading provider of Advanced Process Control & Process Optimization solutions for heavy industries, and particularly for the Cement Industry Our breakthrough AI/APC technologies, customized to our client’s process needs, significantly improve product quality, increase efficiency and output, and decrease costsMar 15, 2017· Cement manufacturing process components of a cement plant from quarry to kiln to cement millCement Manufacturing Process Simplified Flow Chart
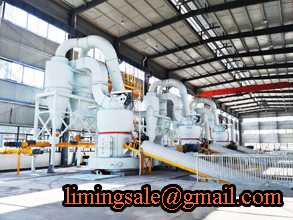
Explain dry and wet process of cement manufacturing
Dec 13, 2018· The flowsheet diagram of the wet process for manufacturing Portland cement is given in Figure 33 The limestone is disintegrated in crushers The crushed limestone is fed to tube mill, where the limestone and the clay, introduced as a slurry from aFlow Diagram of Cement Manufacturing Process then fed to the raw mill inlet with the help of belt conveyors Two types of Raw Mills are used for grinding raw material ie ball mill and vertical roller mill (VRM) The VRM combines the drying, grinding and separation processes into just one unitCHAPTER 30 CEMENT MANUFACTURING PROCESS
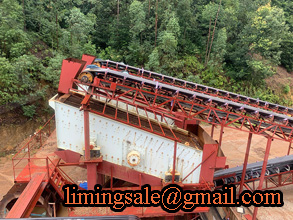
Cement Production Process LinkedIn SlideShare
Sep 17, 2015· The output of a cement mill is the final product viz Cement The term bag house is applied to large filters containing a number of tubular bags mounted in a usually rectangular casing The dust laden air is drawn through them by suction 14 15 Cement Storage Silo The cement storage silo is used for storing the finished product – cement 16For cement packing, cloth, jute, and highdensity Polythene (HDPE) bags are commonly used For convenience, the cement comes to the customer in bags containing measured quantity The standard bag of cement as distributed in India is commonly 50 kg or 112 5 lbs 2 Wet Process of Manufacturing of CementCement Manufacturing Process: What is Cement made of
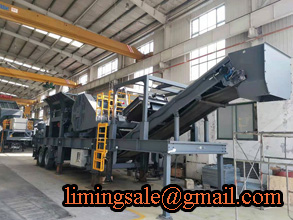
(PDF) Energy audit of thermal utilities in a cement plant
CEMENT MILL In cement process this is the final s tage The typical coal mill circuit diagram with temperature, pressure, oxygen percentage and flow of fans at various locations is Cement manufacturing is a complex process that begins with mining and then grinding raw materials that include limestone and clay, to a fine powder, called raw meal, which is then heated to a sintering temperature as high as 1450 °C in a cement kiWhat is the manufacturing process of cement? Quora
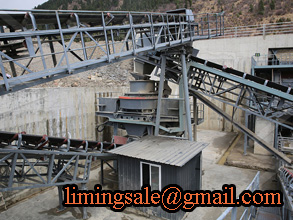
CEMENT PRODUCTION AND QUALITY CONTROL A Cement
additive) are proportioned and ground in Cement mill (one Closed circuit ball mill in line 1 and two Roller press+closed circuit ball mill in line 2) based on the type of cement to be produced keeping the quality of cement equal or above the required standard For instance (Clinker+Pozzolana+Gypsum) are proportioned and milledDiagram of cement ball mill (Based on an image from ThyssenKrupp AG 15) Much of the energy consumed by a ball mill generates heat Water is injected into the second chamber of the mill to provide evaporative cooling Air flow through the mill is one medium for cement transport but also removes water vapour and makes some contribution to coolingBall Mills an overview | ScienceDirect Topics
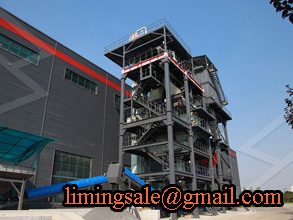
Cement Manufacturing Process Simplified Flow Chart
Mar 15, 2017· Cement manufacturing process components of a cement plant from quarry to kiln to cement millCement manufacturing: components of a cement plant This page and the linked pages below summarize the cement manufacturing process from the perspective of the individual components of a cement plant the kiln, the cement mill etc For information on materials, including reactions in the kiln, see the ' Clinker ' pagesCement manufacturing components of a cement plant
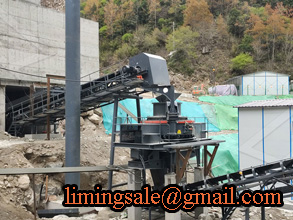
ES Processing | Advanced Process Control and Process
ES Processing is a leading provider of Advanced Process Control & Process Optimization solutions for heavy industries, and particularly for the Cement Industry Our breakthrough AI/APC technologies, customized to our client’s process needs, significantly improve product quality, increase efficiency and output, and decrease costsvertical cement mill diagram – CGM Grinding Plant Sectional diagram of a FullcrLoesche vertical roller mill gas flow outside of a vertical mill; Diagram 5hydraulic systems for ball mills »More detailedloesche vertical roller mill hydraulic system flow diagram
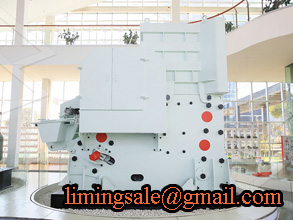
“BEST AVAILABLE TECHNIQUES” FOR THE CEMENT INDUSTRY
Cement Plants Cement Plants (with kilns) (with cement mills only) Austria 11 1 Belgium 5 3 Denmark 1 – Finland 2 – France 38 5 Germany 50 20 Greece 8 – Ireland 2 – Italy 64 29 Luxembourg 1 1 Netherlands 1 2 Portugal 6 1 Spain 37 5 Sweden 3 – United Kingdom 23 1 Total 252 68 Table 23: Number of cement plants in EU countries (1995)May 02, 2019· Take 1012 old books that you won't read anymore and mix a bowl of cement Put the books in the cement mixture one by one and then place them one on another randomly to35 CEMENT IDEAS THAT ARE SO EASY