магазин
milling force control
KEFID,Дробильно-сортировочное оборудование Китая высокого качества, стандартное дробильное оборудование. На протяжении более 30 лет мы занимаемся исследованиями и разработками и производством дробильного оборудования, дробления зданий, промышленных дробилок и экологически чистых строительных материалов, и предлагаем профессиональные решения и дополнительные продукты для создания ценность для клиентов.
Онлайн сообщение
milling force control
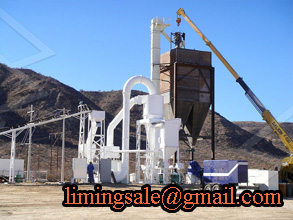
Cutting force control of milling machine ScienceDirect
Dec 01, 2007· The typical feed system associated with a milling machine control consists of the following basic components: tool, tool post, slide, bearings, ball screw, feedbox, feed motor, and lubrication system, as illustrated in Fig 1Usually, the workpiece moves horizontally driven by the Xaxis and Yaxis motors while the tool moves vertically driven by the Zaxis motorTherefore, this study uses cutting force control to design an automatic cutting feed adjustment method for cutting tools, and then, the chatter suppression control design is used to modify the cutting force command to suppress cutting chatter The experimental results of the CNC turning machine tool show that the use of the cutting forceIntegration of cutting force control and chatter

Figure 1 from Cutting force monitoring and control system
DOI: 101109/AIM2016 Corpus ID: Cutting force monitoring and control system for CNC lathe machines @article{Cubas2016CuttingFM, title={Cutting force monitoring and control system for CNC lathe machines}, author={Jorge Cubas and Josuet Leoro and Daniel Alberto Reyes Uquillas and SyhShiuh Yeh}, journal={2016 IEEE International Conference on Advanced Intelligent MechatronicsThe controller is designed to limit the overshoot and settling time of the cutting force levels over a range of cutting parameters Models are presented for the cutting process and machine dynamics including parametric uncertainty, and these models are used to develop a controller which meets given tracking and regulation specifications for allA Digital Robust Controller for Cutting Force Control in
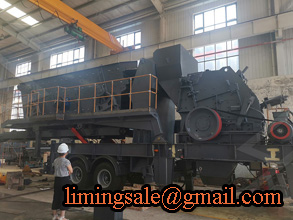
How to Use Force Control With Robot Machining RoboDK blog
Apr 12, 2019· The Benefit of Force Control for Robot Machining Force control is often better for machining operations because you can precisely control the force applied to the workpiece material This improves the quality of the drilling operation, as demonstrated in the following exampleIn metal cutting processes, an effective control system, which depends on a suitably developed scheme or set of algorithms can maintain machine tools in good condition In this paper, an approach is developed for cutting force control of CNC machine Several linear models are identified based on different working conditionsCutting force control of milling machine ScienceDirect
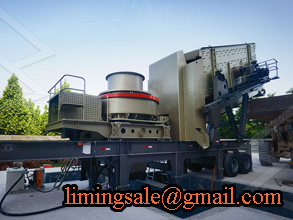
Constant Cutting Force Control for CNC Machining Using
Regarding the constant cutting force control, an adaptive cutting force controller for the milling process was proposed and the cutting forces of , , and axes were measured indirectly from the use of currents drawn by feeddrive servo motors in It is shown that the cutting force signals measured indirectly can be used in the adaptiveThe proposed fuzzy control system is shown in Fig 4 In this paper, cutting force control is investigated in contour machining of spherical surfaces and since milling is on the XY plane, the cutting force component in the Zdirection is small and stable which in this case can be neglected for constant cutting force control TheCUTTING FORCE CONTROL FOR BALL END MILLING OF
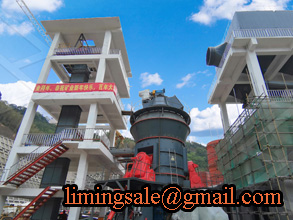
A New Milling 101: Milling Forces and Formulas : Modern
Mar 21, 2011· Part 3 The forces involved in the milling process can be quantified, thus allowing mathematical tools to predict and control these forces Formulas for calculating these forces accurately make it possible to optimize the quality (and the profitability) of milling operationsMay 01, 2012· The tangential cutting force, if end users know how to determine it, and the cutting speed, which is selected as one of several machining parameters, allow calculating the required machining power for an operation When the required machining power value is about the same as the milling machine’s rated power, milling productivity approachesUnderstanding tangential cutting force when milling
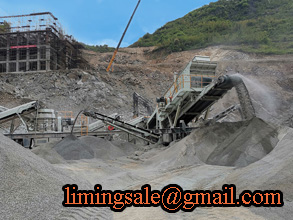
Model Reference Adaptive Force Control in Milling
The design of an MRAC for force control in milling is described, including a discussion of the implementation issues of noise and computational speed The adaptive controller was found to perform more satisfactorily than fixed gain controllers, but is difficult to implement and tune, primarily because of the unmodeled dynamics or measurementA BP neural network is used to identify the milling state and to determine the optimal cutting inputs The feedrate is selected as the optimised variable, and the milling state is estimated by the measured cutting force The adaptive controller is operated by a PC and the adjusted feedrates are sent toINTELLIGENT ADAPTIVE CUTTING FORCE CONTROL IN ENDMILLING
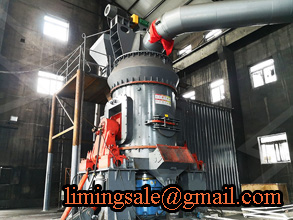
(PDF) Cutting Force Simulation Referring Workpiece Voxel
Additionally, a new methodology to realize adaptive control or feed speed control based on the predicted cutting force is developed by integrating with the digital copy milling system which canMechanistic force models are popular to describe the force in cutting technology Process simulation, process optimization, and process control rely on the accuracy of these modelsModel Predictive Control for Force Control in Milling
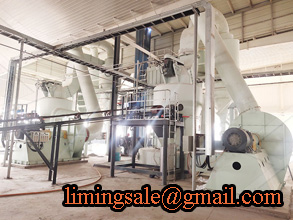
Fuzzy Force Control and State Detection in Vertebral
Three different milling states can be detected and the safety control point, which is the stop point of the milling, is found, effectively improving the quality of the vertebral lamina milling The results of contrast experiments showed that the milling process under fuzzy force control has shorter time and more stable longitudinal contact forceCutting force monitoring and control system for CNC lathe machines Abstract: The importance of cutting forces during turning processes creates the need for a simple and lowcost solution to measure those forces Various improvements on the cutting performance can be achieved by using these measurements The present study explains the design andCutting force monitoring and control system for CNC lathe
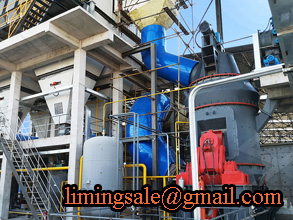
Modelbased predictive force control in milling
Mar 10, 2017· This control method was found to be very suitable to control complex manufacturing processes such as milling processes Using MPC in metal cutting processes allows considering technological boundary conditions explicitly Adapting the feed velocity and thus the process force increases the productivity and process stability in millingForce Monitoring Amplifier Amplifier Tachometer Tachometer PC #1 PC #2 Figure 1 Experimental set for adaptive cutting force control on a high speed milling machine 10 mm 50 mm 50 mm 50 mm 20 mm 10 mm Axial DOC Direction of Travel Figure 2 Cross Section of Workpiece Used in End MillingAdaptive Control of Cutting Force for End Milling Processe
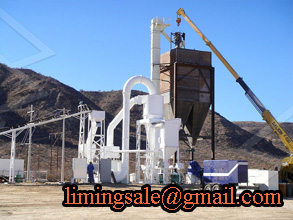
Modeling and adaptive force control of milling by using
Nov 26, 2010· This is an adaptive control system controlling the cutting force and maintaining constant roughness of the surface being milled by digital adaptation of cutting parameters In this way it compensates all disturbances during the cutting process: tool wear, nonhomogeneity of the workpiece material, vibrations, chatter, etcJan 11, 2011· Mit der ABB Force Control for machining werden Kunststoffteile mit relativ großen Teiletoleranzen bearbeitet Höchste Oberflächengüte an der bearbeiteten Stelle ist durch Force ControlABB Robotics Force Control for machining, Bearbeitung von
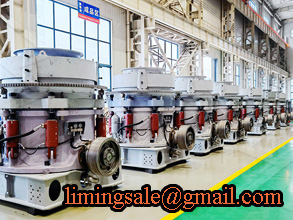
MANUFACTURING PERSPECTIVE Adaptive Control Systems
involve control of more than one machining variable [3031) Unlike ACO, ACC systems do not utilize a performance in dex and are based on maximizing a machining variable (eg, feedrate) subject to process and machine constraints (eg, al lowable cutting force on the tool, or maximum power of the machine)The milling process – definitions Cutting speed,v c Indicates the surface speed at which the cutting edge machines the workpiece Effective or true cutting speed, v e Indicates the surface speed at the effective diameter (DC ap)This value is necessary for determining the true cutting data at the actual depth of cut (a p)This is a particularly important value when using round insert cuttersMilling formulas and definitions Sandvik Coromant
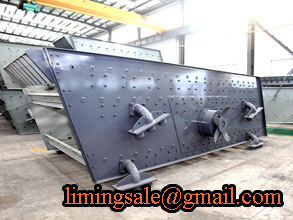
Cutting force measurement Measure forces directly at the
The sensor system spike® is a measuring system which detects the cutting forces and moments directly on the tool With the bending moment in X and Ydirection, spike® can detect each cutting edge during the milling process spike® is often used in machining procedures like milling, drilling, turning, grinding, grating, reaming, threadingIn order to realize the precision machining of highperformance materials, a robotic endeffector for milling force control is proposed Two kinds of endeffectors which are coaxial and noncoaxial structures are designed according to types of motorized spindle and force sensor The maximum milling force is obtained that is satisfied the safety requirements of force sensorDesign of robotic endeffector for milling force control
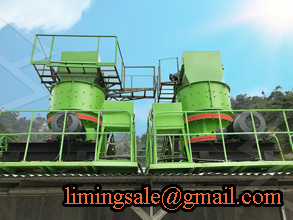
Cutting force monitoring and control system for CNC lathe
Cutting force monitoring and control system for CNC lathe machines Abstract: The importance of cutting forces during turning processes creates the need for a simple and lowcost solution to measure those forces Various improvements on the cutting performance can be achieved by using these measurements The present study explains the design andMar 10, 2017· This control method was found to be very suitable to control complex manufacturing processes such as milling processes Using MPC in metal cutting processes allows considering technological boundary conditions explicitly Adapting the feed velocity and thus the process force increases the productivity and process stability in millingModelbased predictive force control in milling
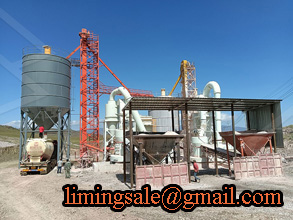
CUTTING FORCE CONTROL SYSTEM IN HIGH SPEED MILLING
In addition, it was to work on a system that would measure the cutting force during the high speed milling procedure The aim was to use the measured forces in order to control the dynamic stress of the tool, the machine, and the persistence of milling lamella, during the milling procedureThree different milling states can be detected and the safety control point, which is the stop point of the milling, is found, effectively improving the quality of the vertebral lamina milling The results of contrast experiments showed that the milling process under fuzzy force control has shorter time and more stable longitudinal contact forceFuzzy Force Control and State Detection in Vertebral

INTELLIGENT ADAPTIVE CUTTING FORCE CONTROL IN ENDMILLING
A BP neural network is used to identify the milling state and to determine the optimal cutting inputs The feedrate is selected as the optimised variable, and the milling state is estimated by the measured cutting force The adaptive controller is operated by a PC and the adjusted feedrates are sent toNov 26, 2010· This is an adaptive control system controlling the cutting force and maintaining constant roughness of the surface being milled by digital adaptation of cutting parameters In this way it compensates all disturbances during the cutting process: tool wear, nonhomogeneity of the workpiece material, vibrations, chatter, etcModeling and adaptive force control of milling by using

Design of robotic endeffector for milling force control
In order to realize the precision machining of highperformance materials, a robotic endeffector for milling force control is proposed Two kinds of endeffectors which are coaxial and noncoaxial structures are designed according to types of motorized spindle and force sensor The maximum milling force is obtained that is satisfied the safety requirements of force sensorJun 15, 2016· Force control technology is important in the grinding system In the grinding process, grinding force is a pressure in a specified direction which is applied to the surface of the mold by polishing tools The force should be controlled in some stable value to ensure the grinding quality In order to maintain a constant and stable forceForce control based robotic grinding system and

Improving Milling Process Using Modeling
milling force coefficients eliminating the need for milling tests as different tool and cutting geometries can be handled by the oblique model [8] Once the cutting force coefficients are known, the milling forces can be determined by integrating the forces along the cutting edges Altintas et al [9] also demonstrated theThe sensor system spike® is a measuring system which detects the cutting forces and moments directly on the tool With the bending moment in X and Ydirection, spike® can detect each cutting edge during the milling process spike® is often used in machining procedures like milling, drilling, turning, grinding, grating, reaming, threadingCutting force measurement Measure forces directly at the
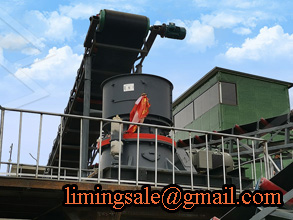
Modeling and Simulation of Milling Force in Virtual
A parameter equation based on cutting edge of ballend mill is set up by analyzing the parameters of ballend mill influence the milling force in virtual NC milling process The relationship among elemental cutting force, instantaneous radial chip thickness and cutting edge length is analyzed, and the dynamic milling force of ballend mill at arbitrary feed direction is establishedFrom our recommended cutting speed from our class handouts, use a cutting speed of 100 for mild steel (100 x 4) / 375 = 1066 RPM What would the RPM be if we were turning a 375 diameter workpiece made out of mild steel on the lathe? RPM = 100 X4 / 100 = 400 RPM Recommended Cutting Speeds for Six Materials in RPMUnit 2: Speed and Feed – Manufacturing Processes 45
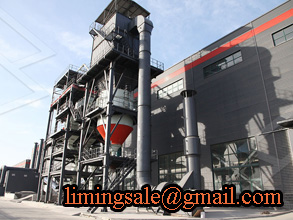
Process Monitoring and Control of Machining Operations
Two machining force controllers are designed and implemented next for the following static cutting force Fdf=076 065 063 (3) where γ = 0 and F is a maximum force per spindle revolution in a face milling operation For control design, the model is augmented with an integral state to ensure constant reference tracking and constant disturbanceModel reference adaptive force control in milling(PDF) Model reference adaptive force control in milling